RIM: A Pillar of Efficient Plastic Manufacturing
2024-12-12 14:04:34
Source:cfz
Low-pressure injection molding, known as Reaction Injection Molding (RIM), is an advanced manufacturing process that combines chemical reactions with injection molding technology. Renowned for its efficiency, cost-effectiveness, and superior performance, it is widely applied in industries such as automotive, medical devices, and electronics. With its unparalleled advantages in producing complex and high-strength plastic components, RIM has become a cornerstone of modern manufacturing.
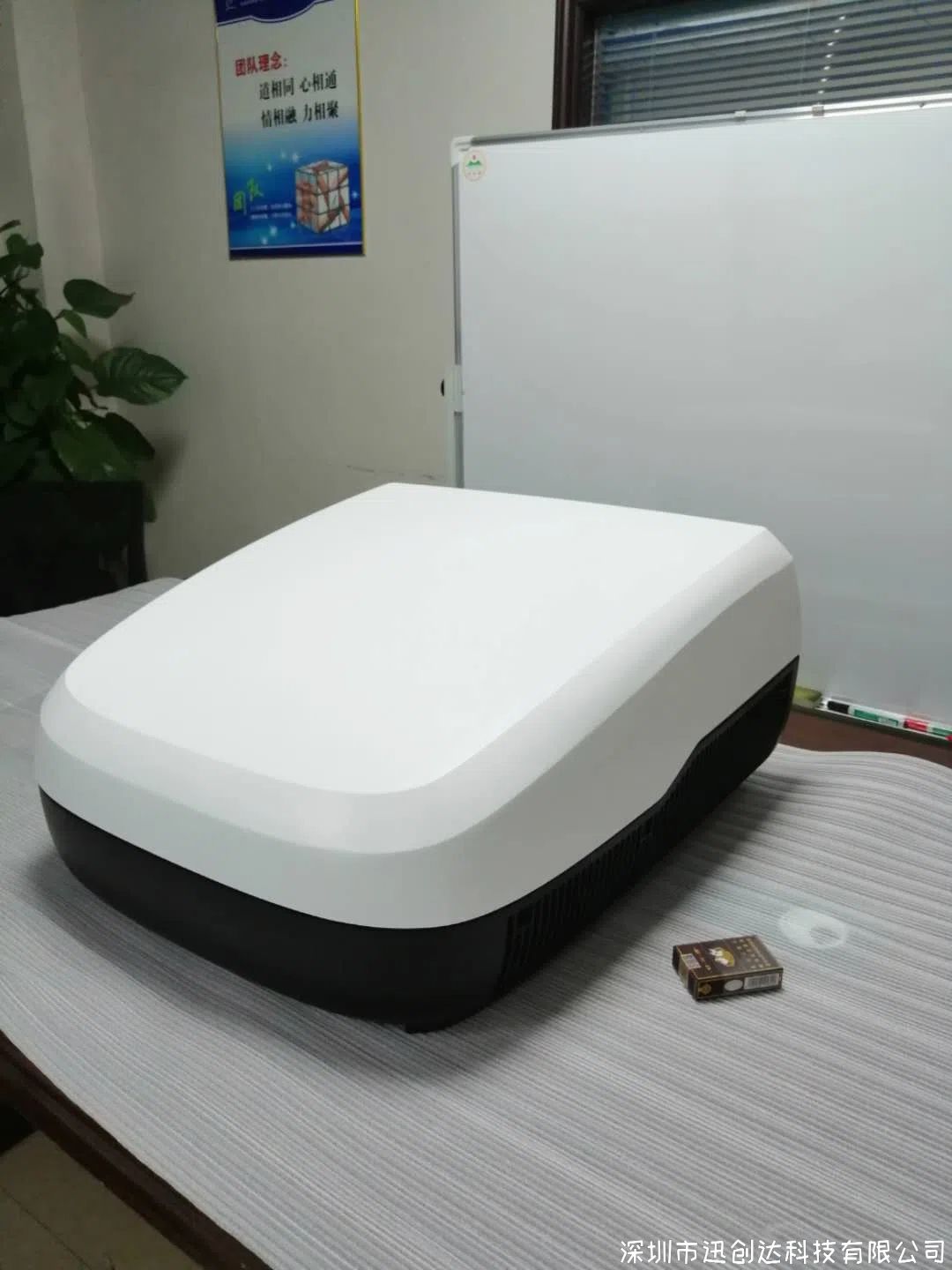
The Principles of Low-Pressure Injection Molding
At the heart of the RIM process is the low-pressure injection of two or more reactive liquid materials (e.g., polyurethane or epoxy resin) into a mold. Within the mold cavity, these materials undergo rapid polymerization and cross-linking reactions, solidifying into the desired shape. This method is particularly suited for manufacturing lightweight, high-strength, and complexly shaped plastic components.Key Steps in the RIM Process
1. Preparation of Raw Materials- Liquid reactive materials, such as polyol and isocyanate, are precisely proportioned.- The materials are stored in separate heated tanks, maintaining consistent temperatures and homogeneity.2. Mixing and Injection- Using high-precision metering equipment, the raw materials are delivered to the mixing head.- In the mixing head, the components are blended rapidly and then injected into the mold under low pressure.3. Chemical Reaction Inside the Mold- Once injected, the materials immediately begin a chemical reaction, solidifying into the desired product.- Depending on the thickness and material properties, the curing process typically takes 30 seconds to a few minutes.4. Demolding and Post-Processing- After curing, the mold is opened, and the finished product is removed.- Post-processing steps, such as surface finishing, painting, or other treatments, are carried out as needed.Distinct Advantages of Low-Pressure Injection Molding
1. Extended Mold Life and Lower Equipment CostsThe low-pressure injection process reduces mechanical stress on the mold, extending its service life and lowering equipment investment and maintenance costs.2. Versatility for Complex DesignsRIM is highly adaptable, making it ideal for producing large, complex, and thick-walled components with ease.3. High Efficiency and Material SavingsThe rapid chemical reaction enables shorter molding cycles, while precise material usage minimizes waste.4. Superior Product PropertiesRIM components often exhibit exceptional mechanical qualities, including high impact resistance, excellent dimensional stability, and outstanding weather resistance.Major Applications of RIM Technology
- Automotive Industry: Used to manufacture bumpers, dashboards, and other components that meet the demands for lightweight and durable designs.- Electronics: Produces heat-resistant and highly insulated enclosures and components.- Medical Devices: Fabricates corrosion-resistant and intricately designed outer casings.- Home Appliances: Creates sturdy and aesthetically pleasing structural parts and panels.Future Trends: A Path Toward Sustainability and Intelligence
As the manufacturing industry moves toward greener and smarter production, RIM technology is evolving in the following directions:- Development of Eco-Friendly Materials: Innovating new polymer systems to reduce environmental impact and minimize harmful chemicals.- Digitalization and Automation: Enhancing production efficiency and consistency through digital monitoring systems and intelligent equipment.Conclusion
Low-pressure injection molding (RIM) has established itself as a critical technology in plastic manufacturing, offering high efficiency and unparalleled flexibility. Looking ahead, ongoing innovations will enable RIM to deliver even more competitive and sustainable solutions, driving high-quality and customized production across industries.