Black Oxide Surface Treatment: Process, Applications, and Benefits
2024-10-29 17:12:17
Source:cfz
What is Black Oxide Surface Treatment?
Black oxide surface treatment, often called metal blackening, is a specialized process applied to metals like steel and stainless steel. Through a controlled chemical reaction, the surface of the metal is oxidized, forming a thin black oxide layer. This layer enhances both the visual appeal and the corrosion and wear resistance of the material.This technique, sometimes referred to as black oxide coating or finishing, is widely used in industrial manufacturing to protect and beautify metal parts and tools. One key advantage is that it preserves the metal's original dimensions and mechanical properties, making it suitable for applications where precision is critical.
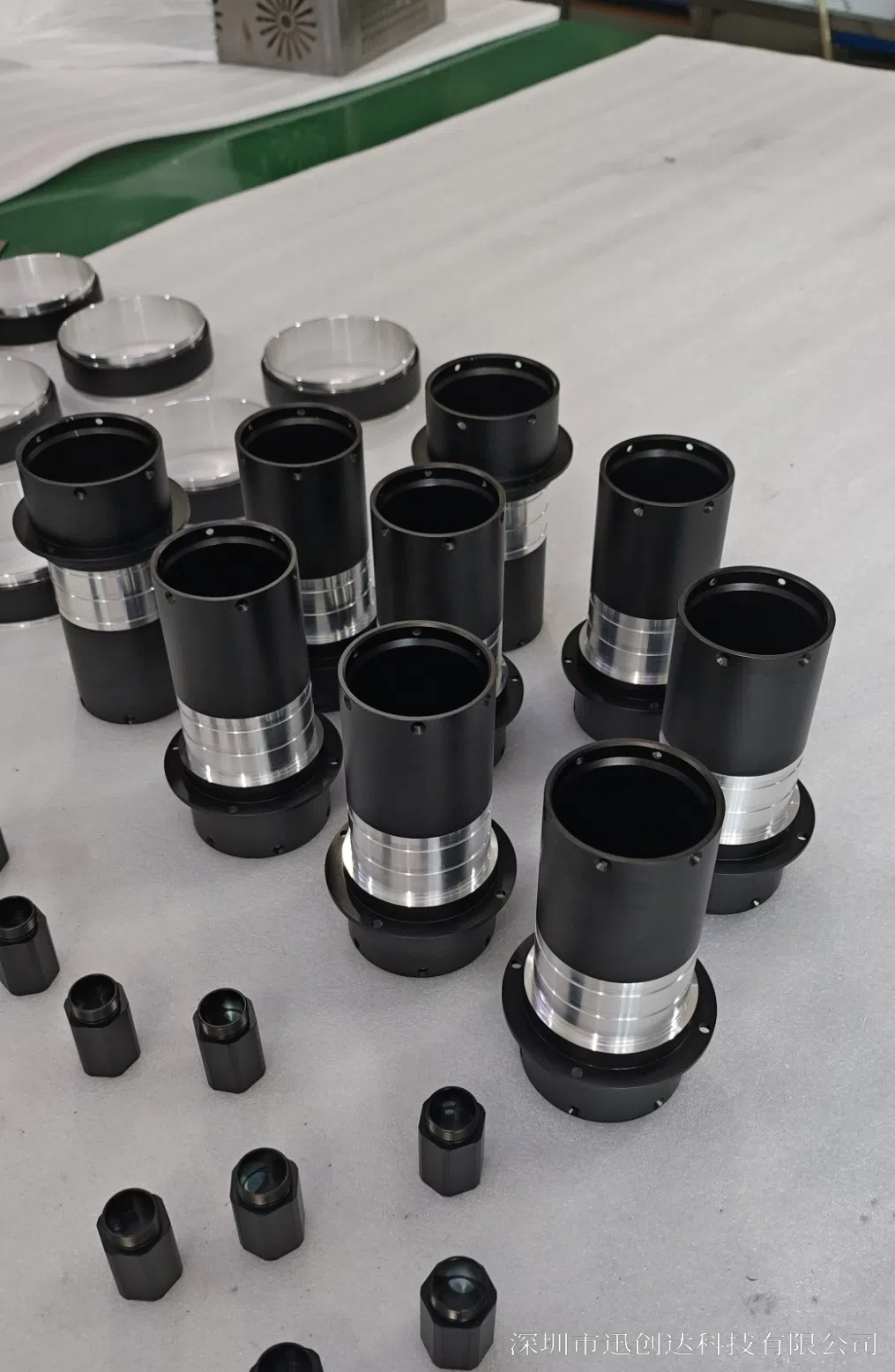
Key Steps in the Black Oxide Process
The black oxide treatment involves several critical steps:1. Cleaning and Degreasing
The metal surface must first be thoroughly cleaned to remove oils, dirt, and other contaminants. This is typically done using chemical degreasers or ultrasonic cleaning systems.2. Acid Pickling
Once cleaned, the metal undergoes acid pickling to remove any remaining oxides and surface impurities. This ensures the metal is ready for the oxidation process.3. Oxidation
The cleaned metal is immersed in a heated solution containing caustic salts and oxidizing agents, typically at temperatures of 140-150°C. This induces the formation of a black iron oxide layer (Fe3O4) that is only a few microns thick.4. Rinsing and Passivation
After oxidation, the metal is rinsed to remove chemical residues, which helps prevent further corrosion. A passivation step may also be applied to enhance the metal’s resistance to oxidation.5. Oiling or Sealing
To provide additional protection and lubricity, the treated metal is often coated with oil or a sealant. This step further improves the metal’s corrosion resistance.Applications of Black Oxide Surface Treatment
Black oxide coatings are employed across various industries, especially where corrosion resistance, wear protection, and enhanced aesthetics are required.Automotive and Aerospace
In these sectors, components often need both corrosion protection and an improved appearance. Black oxide not only shields parts from wear but also provides a low-reflective finish, reducing glare.Machining and Tool Manufacturing
Mechanical components such as gears, bolts, and bearings are commonly treated with black oxide to extend their lifespan by reducing wear and providing built-in lubrication.Military and Defense Equipment
Military gear often requires a non-reflective matte surface with excellent corrosion protection. Black oxide treatment offers an ideal solution for these demanding applications.Medical Devices
Medical instruments, particularly those made of stainless steel, benefit from black oxide treatment, as it increases durability while meeting hygiene standards.Consumer Electronics
In the electronics industry, black oxide treatments are used on metal housings and components to boost corrosion resistance and add a sleek, modern appearance.
Advantages of Black Oxide Surface Treatment
Compared to other surface treatments, black oxide offers several key benefits:Enhanced Corrosion Resistance
While the black oxide layer is thin, when sealed with oil or another protective coating, it significantly improves the material's resistance to corrosion, particularly in humid or mildly corrosive environments.Aesthetic Improvement
The matte black finish created by black oxide is ideal for applications where a non-reflective surface is required. It also helps hide minor surface defects, leading to a more uniform appearance.Dimensional Stability
Since the black oxide layer is extremely thin, it doesn't alter the dimensions of the metal part. This makes it ideal for precision components, unlike some other coatings that might affect tolerances or fits.Improved Wear Resistance and Lubricity
The protective oxide layer reduces friction and enhances wear resistance. When combined with an oil coating, it adds lubricity, allowing moving parts to function more smoothly.Cost-Effectiveness
Compared to other surface finishing methods like plating or painting, black oxide treatment is relatively inexpensive, particularly for mass production. The process is also efficient and eco-friendly.Metals Suitable for Black Oxide Coating
Black oxide treatments are most commonly applied to the following metals:Carbon Steel and Alloy Steel
Carbon and low-alloy steels respond particularly well to the black oxide process, making them ideal for industrial parts and tools.Stainless Steel
Although stainless steel is naturally resistant to corrosion, black oxide treatment enhances its appearance and provides additional protection.Copper and Brass
While less common, copper and brass can also undergo black oxide treatment, producing a similar protective black finish.Conclusion
Black oxide surface treatment is a highly effective and economical method for enhancing the durability and appearance of metal components. Its widespread use in industries ranging from automotive to medical devices demonstrates its versatility and reliability. By choosing the right materials and processes, manufacturers can significantly extend the life of their products and enhance their market competitiveness.